Need Help! with my milling machine
- nooob
- Offline
- Junior Member
-
Less
More
- Posts: 29
- Thank you received: 0
31 Dec 2014 00:31 #54423
by nooob
Need Help! with my milling machine was created by nooob
Hi guys,
im a totally newbie on Linuxcnc, i work on a retrofit for a Chiron Fz12W Machine an had a few questions and problems btw. sorry for my bad Englisch im from Germany
Units: mm
Machine Data:
Model: Chiron FZ12W
Main Spindel: AC Servo 6000Rpm 1024 encoder lines per rev.
X-Axis: AC Servo 4000Rpm 1250 encoder lines per rev. gear ratio 2:1 pitch ballscrew 10mm
Y-Axis: AC Servo 4000Rpm 1250 encoder lines per rev. gear ratio 2:1 pitch ballscrew 10mm
Z-Axis: AC Servo 4000Rpm 1250 encoder lines per rev. gear ratio 2:1 pitch ballscrew 10mm
rapid traverse: X,Y,Z 20000mm/min = 333,3333mm/sec
What i've done so far:
installing Mesa cards and done with the wiring.
2x 5i20 FPGA
1x 7i33TA
5x 7i37 Opto
Software:
Ubuntu 10.04 Linuxcnc 2.6.5
My Problems:
1. The Servos vibrating when no position is commanded so i've not reached the accuracy i need.
2. The Spindle turns very slow when activatet and not stand still.
Questions:
1. for what exactly is the OUTPUT_SCALE?
i´ve found out that when i double it i must double all values from my PID settings.
2. ENCODER_SCALE:
I calculated it like in the descripion so my value was 250 but it doesen't fit with driven distances as i multiplied with 4 it fits so my formula was
1250 Inkr./rev x 0.2 rev/mm x 4 =1000 Inkr./mm
Why multiplied with 4?
what have i done wrong?
Maybe one of you could look at my conifguration files and tell me what i've done wrong or where i have the wrong values im trying to fix my problems for a week now
so i thought i'm better asking professionals like you guys here
im a totally newbie on Linuxcnc, i work on a retrofit for a Chiron Fz12W Machine an had a few questions and problems btw. sorry for my bad Englisch im from Germany

Units: mm
Machine Data:
Model: Chiron FZ12W
Main Spindel: AC Servo 6000Rpm 1024 encoder lines per rev.
X-Axis: AC Servo 4000Rpm 1250 encoder lines per rev. gear ratio 2:1 pitch ballscrew 10mm
Y-Axis: AC Servo 4000Rpm 1250 encoder lines per rev. gear ratio 2:1 pitch ballscrew 10mm
Z-Axis: AC Servo 4000Rpm 1250 encoder lines per rev. gear ratio 2:1 pitch ballscrew 10mm
rapid traverse: X,Y,Z 20000mm/min = 333,3333mm/sec
What i've done so far:
installing Mesa cards and done with the wiring.
2x 5i20 FPGA
1x 7i33TA
5x 7i37 Opto
Software:
Ubuntu 10.04 Linuxcnc 2.6.5
My Problems:
1. The Servos vibrating when no position is commanded so i've not reached the accuracy i need.
2. The Spindle turns very slow when activatet and not stand still.
Questions:
1. for what exactly is the OUTPUT_SCALE?
i´ve found out that when i double it i must double all values from my PID settings.
2. ENCODER_SCALE:
I calculated it like in the descripion so my value was 250 but it doesen't fit with driven distances as i multiplied with 4 it fits so my formula was
1250 Inkr./rev x 0.2 rev/mm x 4 =1000 Inkr./mm
Why multiplied with 4?
what have i done wrong?
Maybe one of you could look at my conifguration files and tell me what i've done wrong or where i have the wrong values im trying to fix my problems for a week now

so i thought i'm better asking professionals like you guys here

Please Log in or Create an account to join the conversation.
- emcPT
-
- Offline
- Platinum Member
-
Less
More
- Posts: 702
- Thank you received: 139
31 Dec 2014 07:46 #54442
by emcPT
Replied by emcPT on topic Need Help! with my milling machine
Hello,
Your problem 1)
When you say vibrating, what is the magnitude of the vibration? With your set up (1250 ppr encoders and 1 turn == 5mm) I would expect between +-0.004 to 0.01mm around the setting point. This of course depends on your motors, drives and settings.
problem 2)
As it is hard to understand with your information, please inform if the spindle works with an analog signal to set its speed. If so, check if you have 0V when it is supposed to have the spindle stooped.
Question 1)
Output scale for the spindle, is in my configuration the max rpm that my spindle reaches. Also, in my configuration (using analog drives) the output scale is equal to the max velocity setting.
Question 2)
The encoder scale is correct. When you say that the machine does not move the correct amount, by what amount it is not correct? Half of what it should move? The double?
It is multiplied by 4 because it is the result of two channels, A and B. Check: www.eeweb.com/blog/jim_miller/understand...ntal-encoder-signals
I hope that this helps to get you going.
Your problem 1)
When you say vibrating, what is the magnitude of the vibration? With your set up (1250 ppr encoders and 1 turn == 5mm) I would expect between +-0.004 to 0.01mm around the setting point. This of course depends on your motors, drives and settings.
problem 2)
As it is hard to understand with your information, please inform if the spindle works with an analog signal to set its speed. If so, check if you have 0V when it is supposed to have the spindle stooped.
Question 1)
Output scale for the spindle, is in my configuration the max rpm that my spindle reaches. Also, in my configuration (using analog drives) the output scale is equal to the max velocity setting.
Question 2)
The encoder scale is correct. When you say that the machine does not move the correct amount, by what amount it is not correct? Half of what it should move? The double?
It is multiplied by 4 because it is the result of two channels, A and B. Check: www.eeweb.com/blog/jim_miller/understand...ntal-encoder-signals
I hope that this helps to get you going.
The following user(s) said Thank You: nooob
Please Log in or Create an account to join the conversation.
- nooob
- Offline
- Junior Member
-
Less
More
- Posts: 29
- Thank you received: 0
02 Jan 2015 22:49 #54494
by nooob
Replied by nooob on topic Need Help! with my milling machine
thx for the Answer,
so in my ini [Axis] section the OUTPUT_SCALE should be like my max velocity
my old value was 10 so it should be 333.33 like my
MAX_VELOCITY = 333.3 ?
and the Spindle part should look like this ?
[SPINDLE_9]
ENCODER_SCALE = 1024.0
OUTPUT_SCALE = 6000
ANGULAR_UNITS = 2.8444
my Spindle Motor's max Rpm is 6000 so Output Scale schould be the same value?
with the old values the axis vibration was araound +-0,002
On another milling machine, a Hermle with Haidenhain cotrol i've noticed that the Axis positions didn't fluctuating. the display shows 3 digits after comma. So should it look at my machine equal? or is a little fluctuation normal, with the old control on my chiron i didn't saw fluctioarion either so the motors should be goog enough.
i try to Tune the axis with the adjustment again as goog as possible and post the results here hopfully it looks better then.
so in my ini [Axis] section the OUTPUT_SCALE should be like my max velocity
my old value was 10 so it should be 333.33 like my
MAX_VELOCITY = 333.3 ?
and the Spindle part should look like this ?
[SPINDLE_9]
ENCODER_SCALE = 1024.0
OUTPUT_SCALE = 6000
ANGULAR_UNITS = 2.8444
my Spindle Motor's max Rpm is 6000 so Output Scale schould be the same value?
with the old values the axis vibration was araound +-0,002
On another milling machine, a Hermle with Haidenhain cotrol i've noticed that the Axis positions didn't fluctuating. the display shows 3 digits after comma. So should it look at my machine equal? or is a little fluctuation normal, with the old control on my chiron i didn't saw fluctioarion either so the motors should be goog enough.
i try to Tune the axis with the adjustment again as goog as possible and post the results here hopfully it looks better then.
Please Log in or Create an account to join the conversation.
- emcPT
-
- Offline
- Platinum Member
-
Less
More
- Posts: 702
- Thank you received: 139
03 Jan 2015 03:19 #54506
by emcPT
Replied by emcPT on topic Need Help! with my milling machine
Regarding the output scale being 333.3, I think that it is correct if you want a speed of 20 m/min.
In my INI, for example is 167 (10 m/min) and I have several parameters with this value:
MAX_VELOCITY = 167
MAX_OUTPUT = 167
OUTPUT_SCALE = 167
OUTPUT_MIN_LIMIT = -167
OUTPUT_MAX_LIMIT = 167
Regarding the spindle, I also have:
OUTPUT_SCALE = 2500
OUTPUT_MIN_LIMIT = -2500
OUTPUT_MAX_LIMIT = 2500
That in my case is 2500 rpm. I have the encoder scale to match the encoder ppr, so I think you are also correct.
Regarding the fluctuation. If you have 0.002 is not bad at all with your encoders, that have a low resolution. I also have older machines with original controls that only occasionally changed 0.001 (very rare), and I have newer machines - for example a Hurco from 2006 in good condition, that shows more changes on the DRO.
Honestly I believe that a filter is implemented on the controls so that the position is not updated very often in "stand still state".
In my INI, for example is 167 (10 m/min) and I have several parameters with this value:
MAX_VELOCITY = 167
MAX_OUTPUT = 167
OUTPUT_SCALE = 167
OUTPUT_MIN_LIMIT = -167
OUTPUT_MAX_LIMIT = 167
Regarding the spindle, I also have:
OUTPUT_SCALE = 2500
OUTPUT_MIN_LIMIT = -2500
OUTPUT_MAX_LIMIT = 2500
That in my case is 2500 rpm. I have the encoder scale to match the encoder ppr, so I think you are also correct.
Regarding the fluctuation. If you have 0.002 is not bad at all with your encoders, that have a low resolution. I also have older machines with original controls that only occasionally changed 0.001 (very rare), and I have newer machines - for example a Hurco from 2006 in good condition, that shows more changes on the DRO.
Honestly I believe that a filter is implemented on the controls so that the position is not updated very often in "stand still state".
Please Log in or Create an account to join the conversation.
- newbynobi
-
- Offline
- Platinum Member
-
Less
More
- Posts: 2082
- Thank you received: 413
03 Jan 2015 08:21 #54516
by newbynobi
Replied by newbynobi on topic Need Help! with my milling machine
If he lower the deadband in his PID settings, the axis will stand still, but without config files it is a look in the glas ball.
The spindle movement should be stoped with a setting on the amplfier, mine has a Potentiometer.
Regards from Hildesheim von Norbert
The spindle movement should be stoped with a setting on the amplfier, mine has a Potentiometer.
Regards from Hildesheim von Norbert
Please Log in or Create an account to join the conversation.
- nooob
- Offline
- Junior Member
-
Less
More
- Posts: 29
- Thank you received: 0
04 Jan 2015 19:57 - 04 Jan 2015 23:55 #54546
by nooob
Replied by nooob on topic Need Help! with my milling machine
Hi thx for the Answers,
i tought i had attached my config files in my first post but it obviously didnt work.
so now i try it again here is the link:
chiron2014.rar
So in the manual iv'e found this about deadband
"DEADBAND = 0.000015 - How close is close enough to consider the motor in position" so is this something eqal like emcPT was calling it a filter for displaying the axis position?.
iv'e forgot to say that i haven't made any changes on my config file since the first post, im going tomorrow to my shop and try out the new values.
i tought i had attached my config files in my first post but it obviously didnt work.
so now i try it again here is the link:
chiron2014.rar
So in the manual iv'e found this about deadband
"DEADBAND = 0.000015 - How close is close enough to consider the motor in position" so is this something eqal like emcPT was calling it a filter for displaying the axis position?.
iv'e forgot to say that i haven't made any changes on my config file since the first post, im going tomorrow to my shop and try out the new values.
Last edit: 04 Jan 2015 23:55 by nooob.
Please Log in or Create an account to join the conversation.
- newbynobi
-
- Offline
- Platinum Member
-
Less
More
- Posts: 2082
- Thank you received: 413
04 Jan 2015 23:07 #54549
by newbynobi
Replied by newbynobi on topic Need Help! with my milling machine
I will not download that file, because the download will be an EXE file, What is that? We are on linux and nay exe file is a risk for windows users, so please do not do that!!!
Just zip the folder, and attach it with the Add File button.
Norbert
Just zip the folder, and attach it with the Add File button.
Norbert
The following user(s) said Thank You: nooob
Please Log in or Create an account to join the conversation.
- nooob
- Offline
- Junior Member
-
Less
More
- Posts: 29
- Thank you received: 0
04 Jan 2015 23:50 - 04 Jan 2015 23:55 #54553
by nooob
Replied by nooob on topic Need Help! with my milling machine
sry didn't test the download last time it didn't work as attachment
now i uploaded it to my own ftp with a directlink
chiron2014.rar
now i uploaded it to my own ftp with a directlink
chiron2014.rar
Last edit: 04 Jan 2015 23:55 by nooob.
Please Log in or Create an account to join the conversation.
- nooob
- Offline
- Junior Member
-
Less
More
- Posts: 29
- Thank you received: 0
08 Jan 2015 15:39 #54746
by nooob
Replied by nooob on topic Need Help! with my milling machine
So i was in my shop and found time to test it,
now here are the results, but im still not happy about it.
I have tuned the servo amplifier that when no value is in PID, the motor doesn't run away it moves perhaps +-0.004mm or so. I get that through fine tuning the Amplifier with the tiny potentiometers for each axis.
in Halscope the line looks good but when i set the P value the motor starts oscillating like in the Picture.
How can i get that ferror smoother?.
In the tutorial from gnipsel.com he had barely no oscillation until the axis make a move, what is my mistake?
now here are the results, but im still not happy about it.
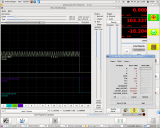
I have tuned the servo amplifier that when no value is in PID, the motor doesn't run away it moves perhaps +-0.004mm or so. I get that through fine tuning the Amplifier with the tiny potentiometers for each axis.
in Halscope the line looks good but when i set the P value the motor starts oscillating like in the Picture.
How can i get that ferror smoother?.
In the tutorial from gnipsel.com he had barely no oscillation until the axis make a move, what is my mistake?
Please Log in or Create an account to join the conversation.
- andypugh
-
- Offline
- Moderator
-
Less
More
- Posts: 23362
- Thank you received: 4964
08 Jan 2015 20:23 #54761
by andypugh
The PID component is not very happy with negative gains.
Change your output scale to -333 and make the gains positive and see if that helps.
Replied by andypugh on topic Need Help! with my milling machine
in Halscope the line looks good but when i set the P value the motor starts oscillating like in the Picture.?
The PID component is not very happy with negative gains.
Change your output scale to -333 and make the gains positive and see if that helps.
The following user(s) said Thank You: nooob
Please Log in or Create an account to join the conversation.
Moderators: piasdom
Time to create page: 0.147 seconds