Planning - Bridgeport Interact 1 linuxCNC Retrofit
- cncnoob1979
-
Topic Author
- Offline
- Platinum Member
-
- Posts: 403
- Thank you received: 75
Please Log in or Create an account to join the conversation.
- andypugh
-
- Offline
- Moderator
-
- Posts: 23362
- Thank you received: 4964
Please Log in or Create an account to join the conversation.
- cncnoob1979
-
Topic Author
- Offline
- Platinum Member
-
- Posts: 403
- Thank you received: 75
Yes I used a 1 1/2 ton engine crane and 10k straps to remove the components.
I used a 6k pallet Jack and a 8k cable hoist to pull it into my garage. I bolted a 1/2 inch concrete wedge anchor into the concrete floor for a pulling point. I had to use the hoist (in the very back of my garage, centered in my garage) due to the fact I have a about a 4 foot 8degree grade into my garage from the driveway. So pushing it was not an option.
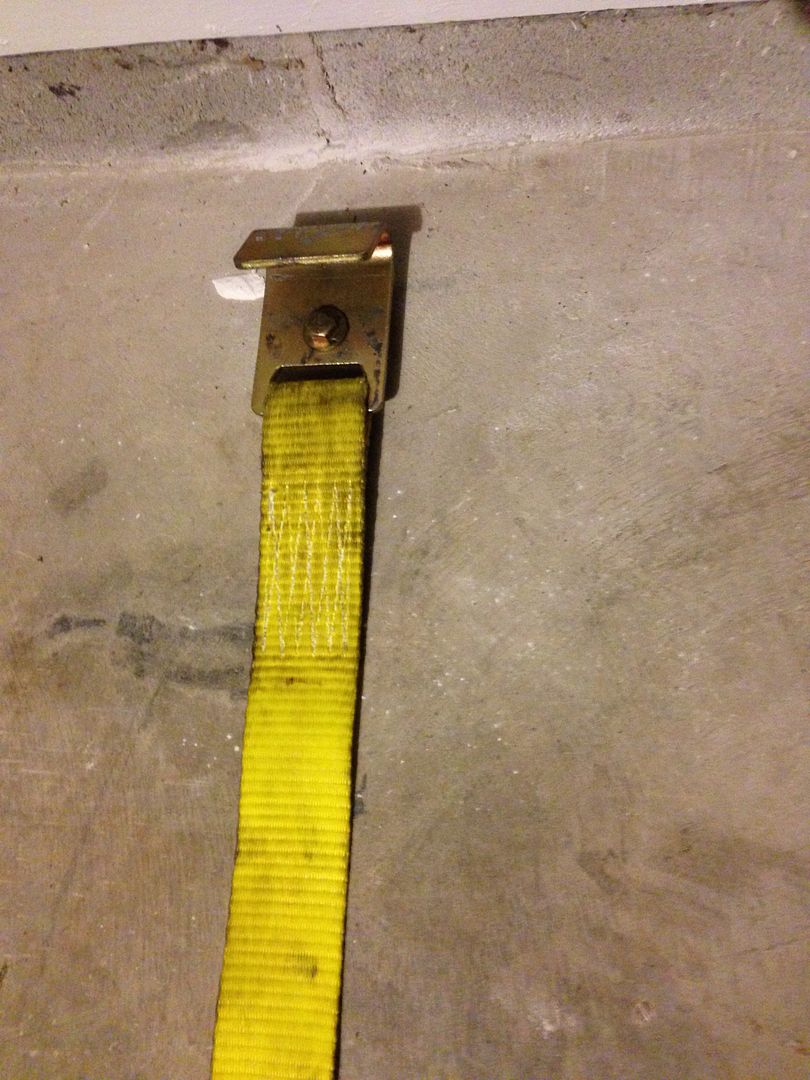
Here is how I attached my sling to the garage floor. I drilled a 1/2 hole into the metal bracket.
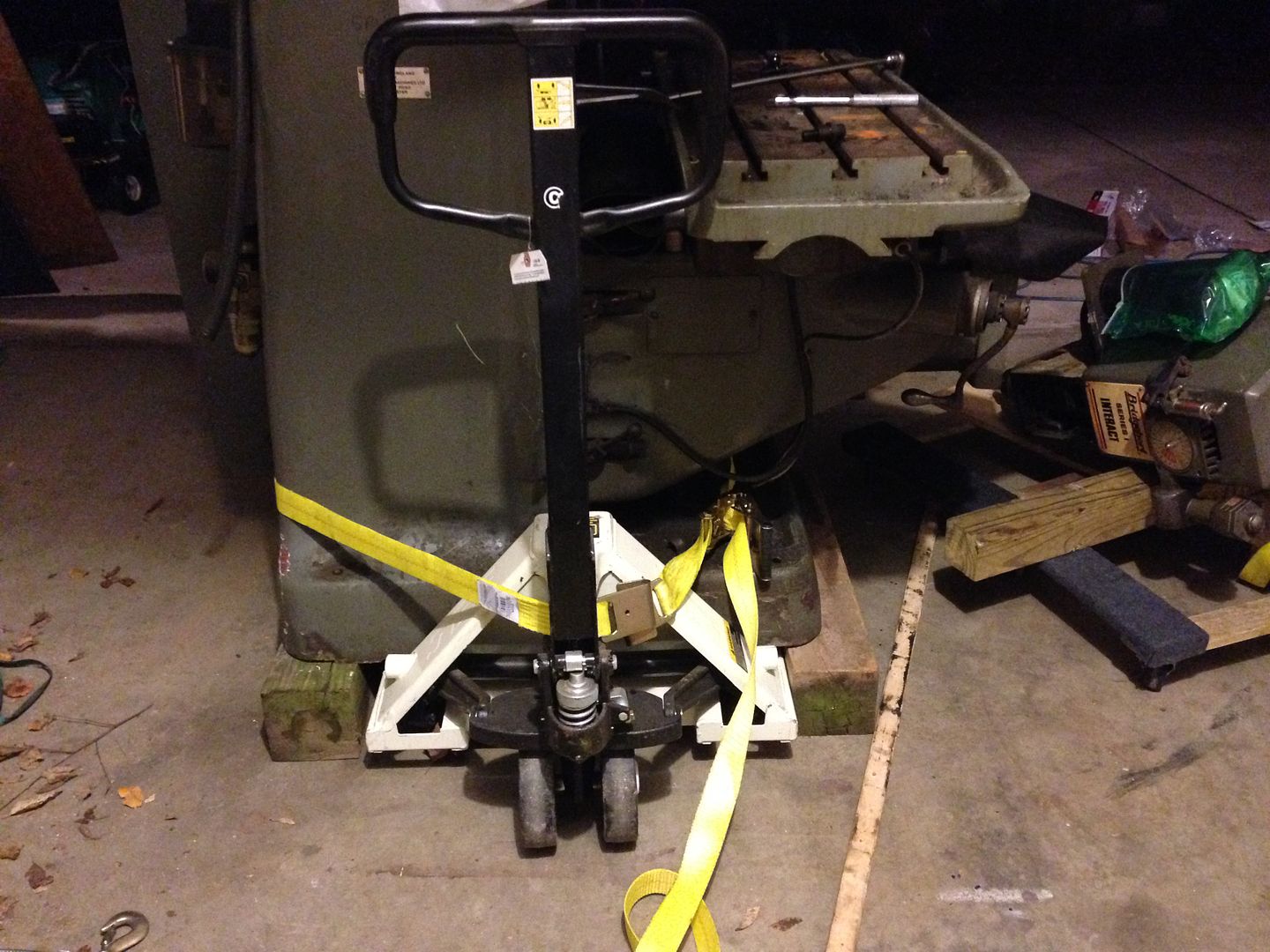
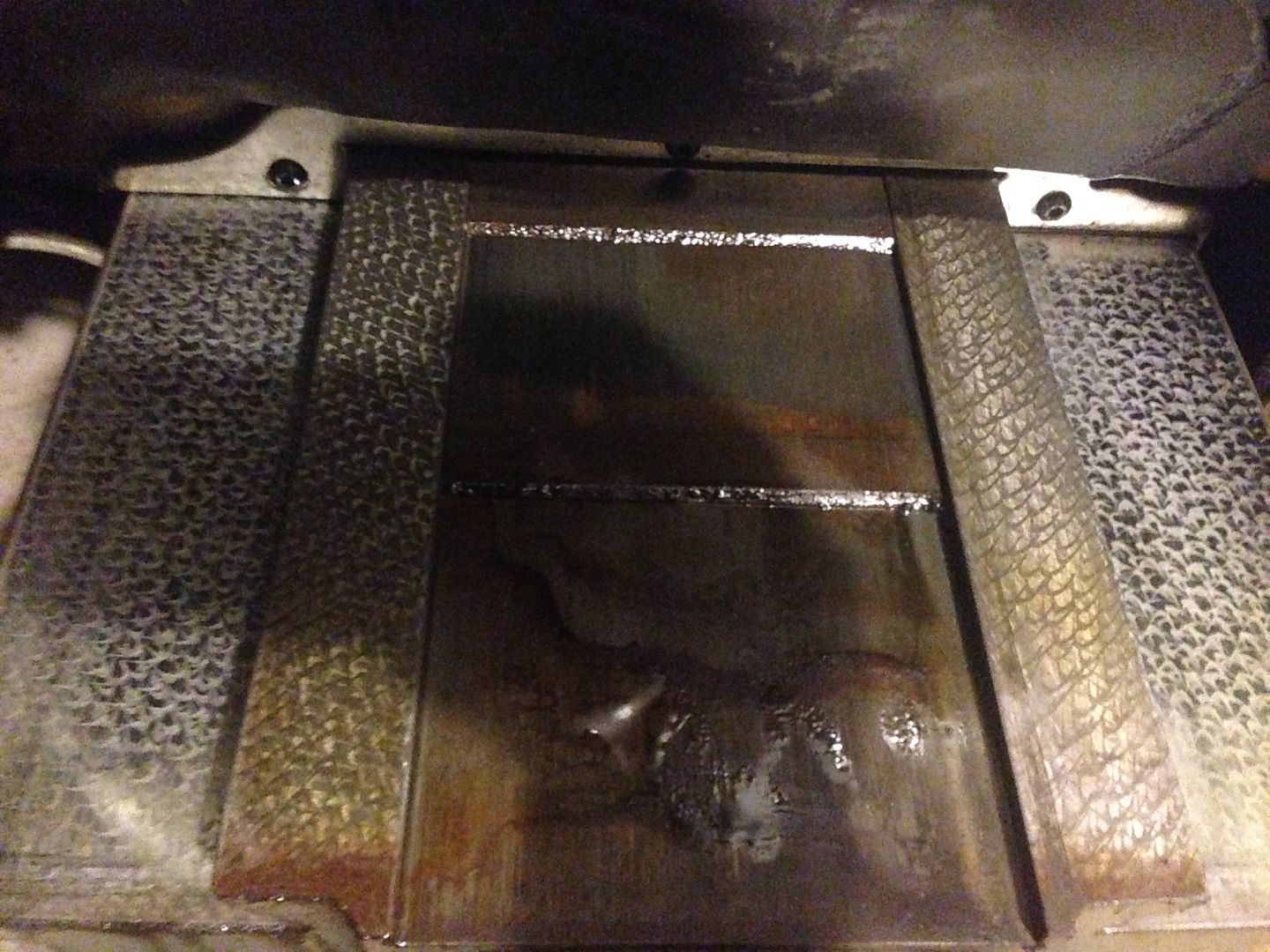
This mill was from a Tech School in Tennessee. Sat in a shop for 6 years before he got rid of it. Looking at the saddle i would say it should be a tight machine.
Please Log in or Create an account to join the conversation.
- andypugh
-
- Offline
- Moderator
-
- Posts: 23362
- Thank you received: 4964
This mill was from a Tech School in Tennessee. Sat in a shop for 6 years before he got rid of it. Looking at the saddle i would say it should be a tight machine.
Looking at the scrape marks it looks like it might never have been used...
Please Log in or Create an account to join the conversation.
- cncnoob1979
-
Topic Author
- Offline
- Platinum Member
-
- Posts: 403
- Thank you received: 75
I'm contemplating acquiring a 3phase converter for this machine, then purchase a VFD for it later.
Would I damage my machine by hooking it up to single phased 220v power? Something to disconnect or remove prior to? Or would it be best to have a 3ph converter first?
Thoughts? Comments? Suggestions?
Please Log in or Create an account to join the conversation.
- cncnoob1979
-
Topic Author
- Offline
- Platinum Member
-
- Posts: 403
- Thank you received: 75
Please Log in or Create an account to join the conversation.
- andypugh
-
- Offline
- Moderator
-
- Posts: 23362
- Thank you received: 4964
Please Log in or Create an account to join the conversation.
- cncnoob1979
-
Topic Author
- Offline
- Platinum Member
-
- Posts: 403
- Thank you received: 75
Andy, the encoders terminate in 9 pin male plugs. I'm considering the exe boxes at the moment.
Most of my connections to the TCN-151 controller was cut. Not much of a bad deal. Also one of my encoder cables were cut. I can just shorten and install to the servo, I have plenty of slack.
The T2 transformer is an auto-transformer from my understanding. In the wiring schematic it shows it as using 103 and 104 as a power source. L1,L2 So I believe this is a step up transformer because the required voltage going to my servo amps require 380v input. Is this accurate? Or am I misreading the schematic?
Please Log in or Create an account to join the conversation.
- andypugh
-
- Offline
- Moderator
-
- Posts: 23362
- Thank you received: 4964
The encoders look like they will plug straight in to those EXE boxes that you bought and then cancelled.Andy, the encoders terminate in 9 pin female plugs. I'm considering the exe boxes at the moment.
So that just leaves the puzzle of finding connectors for the outputs, which Mouser seem to sell at a reasonable price.
The T2 transformer is an auto-transformer from my understanding. In the wiring schematic it shows it as using 103 and 104 as a power source. L1,L2 So I believe this is a step up transformer because the required voltage going to my servo amps require 380v input. Is this accurate? Or am I misreading the schematic?
If it was only L1 and L2 then I would say that you only need to re-arrange the input terminals to suit your mains voltage.
However, I am rather puzzled by the function of the UV inputs which seem like they might be + / - 180 V relative to the 0V line.
Maybe it would be wise to disconnect the outputs, re-arrange the inputs and check output voltages.
Please Log in or Create an account to join the conversation.
- cncnoob1979
-
Topic Author
- Offline
- Platinum Member
-
- Posts: 403
- Thank you received: 75
Well good news. The autotransformer does step up voltage.
In accordance with the schematic I checked 0v line and my 380v line and received around 350v. My L2 (#112) is connected to 210v on the T2 transformer. (Was wired previously for 210 3ph).(I need to move it to the 220) I had to actuate 5FC relay manually to get the power to T2. I haven't figured out what signal to actuate it yet.
Now the bad news. I blew a resistor in my control cabinet upon first actuation of 5FC. (Scared the **** out of me!)
Attached is the resistor I'm currently trying to figure out what it goes to. I think power is heading toward my z axis limit switch wiring. (I had one disconnected and grounded) I think it was a 3R3 prior to me destroying it. But that is from memory.
I'm a child playing pilot in an Airbus here!
Alright. Traced it down to R7, #169 and #7. Guess I took out the z axis power resistor. Now to find a replacement. I think I found the short. I'm at fault. I had the wires hanging from the encoder box but failed to ensure one wasn't grounded. :doh:
Maybe someone should take this machine from me before I destroy it!

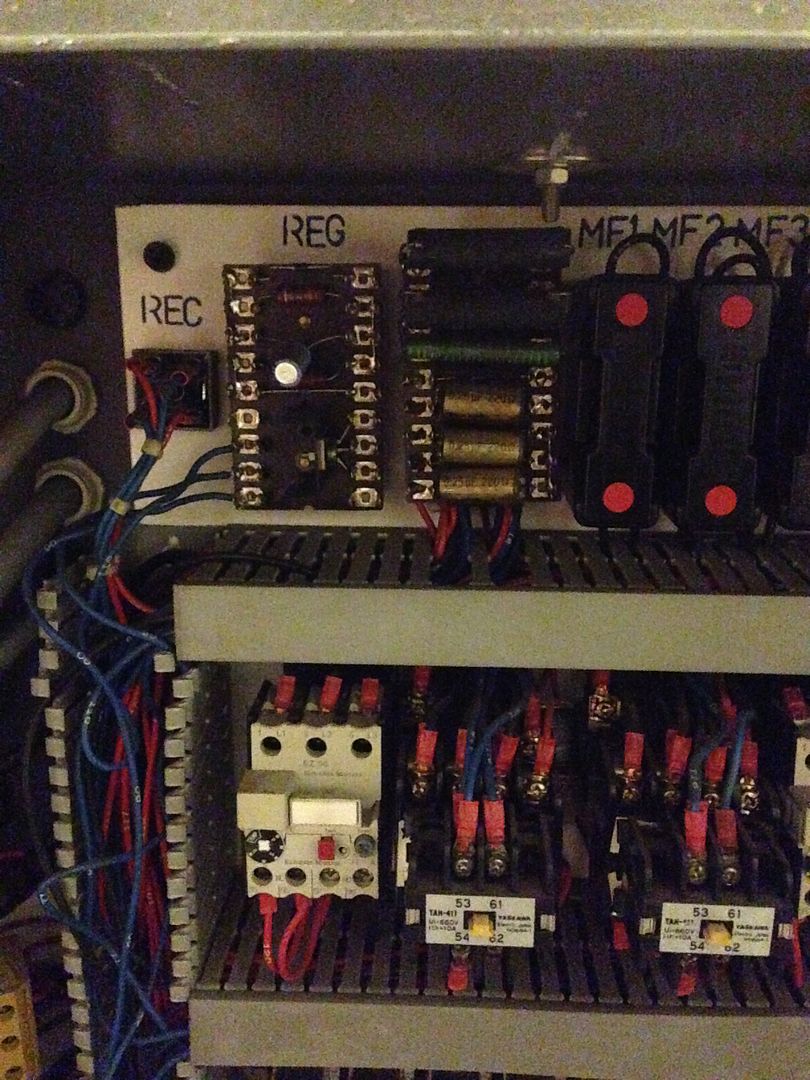
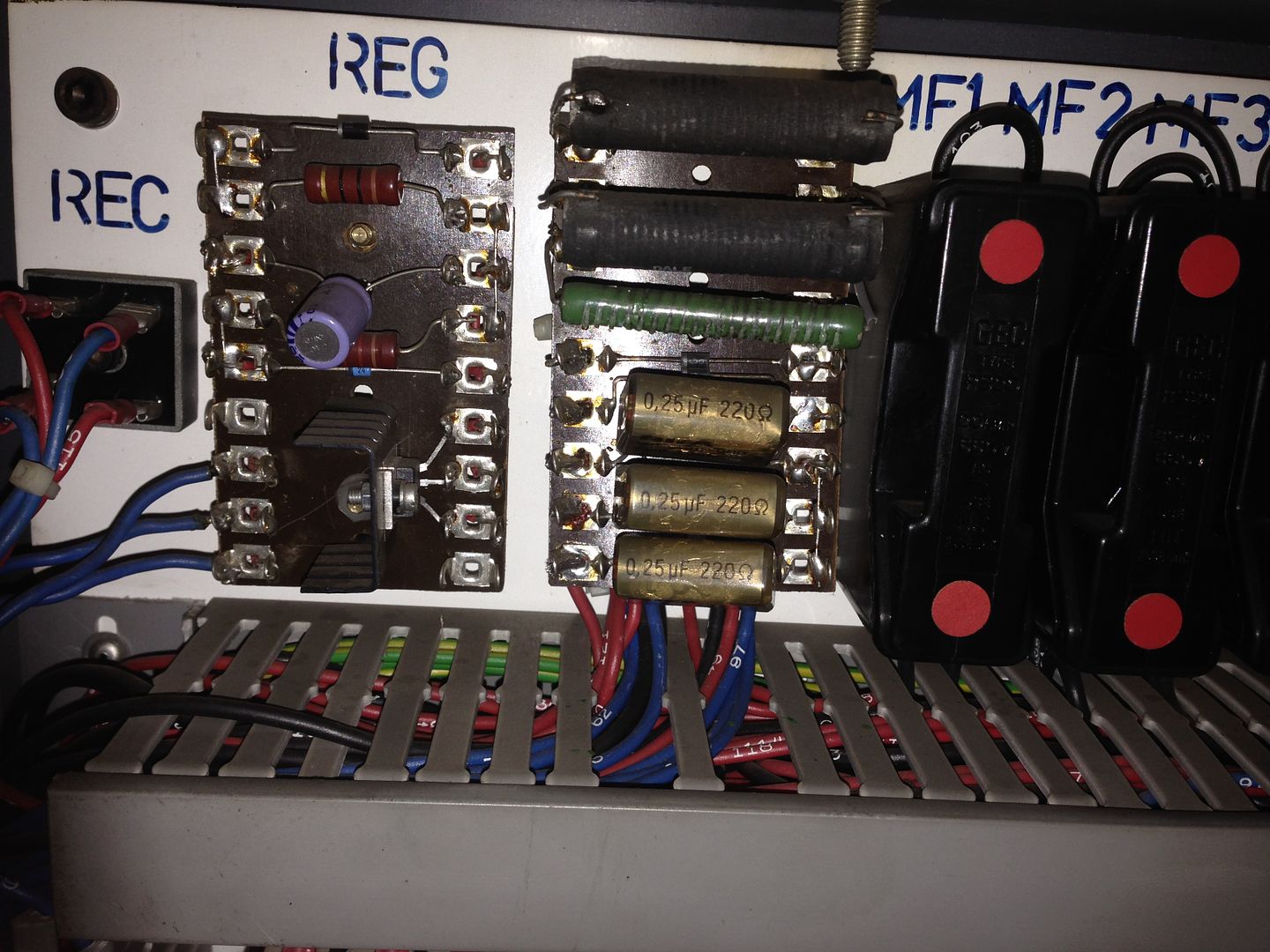
So now the question: where to get a replacement and when the drive amps are powered are the servos immediately powered? I'm pretty sure I tested that. But just incase it should not have happened.
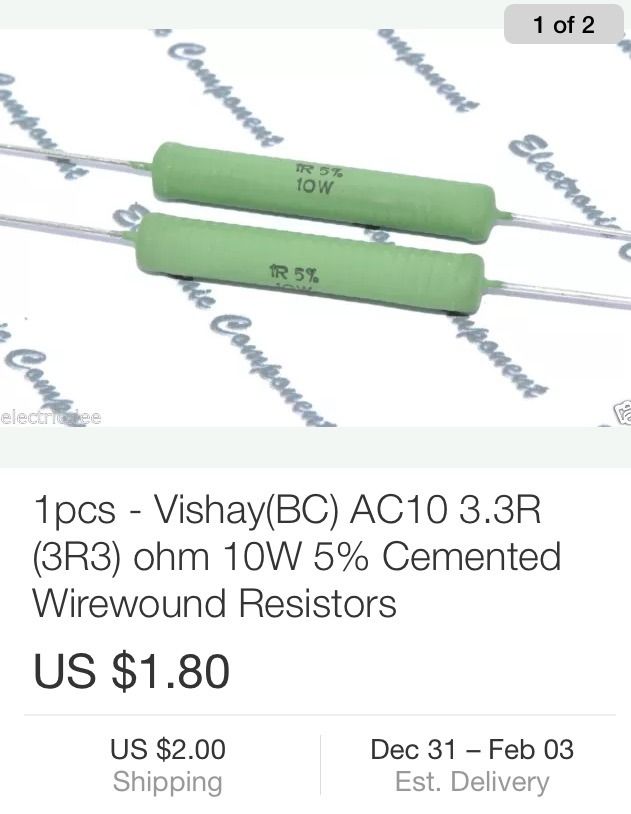
Would this be a suitable replacement?
3.3 ohms/10W
Please Log in or Create an account to join the conversation.